Overview
Automobile manufacturers are the ideal candidates to benefit from Six Sigma quality improvement methodology. Their industry produces a complex product that results from a multitude of manufacturing processes. Auto makers acknowledge the importance of quality not only in producing a profitable product, but also in winning the hearts and minds of their customers. Throughout its history, the automobile industry has provided both good and bad examples of how to implement continuous quality improvement. Today, many auto makers are exemplifying the best way to implement Six Sigma methodology. .
Automobile manufacturers seeking to deploy Six Sigma methodology would do well to follow the lead of organizations that have implemented Six Sigma successfully. Six Sigma must be more than just a passing fad promoted by management. To receive the lasting benefits of Six Sigma, auto makers must have the philosophy engrained in their DNA.
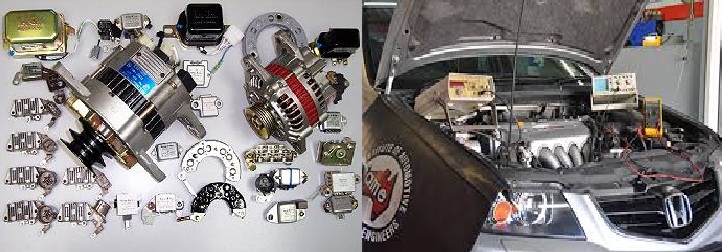
Six Sigma for all
Organizations in the automobile manufacturing industry don’t have to be major players with worldwide corporate concerns to reap the benefits of using Six Sigma. Southland C.N.C. provides precision machined component parts to automobile manufacturers. When Southland set out to expand production capacity by purchasing new hydraulic fixtures, the standard it used to rate equipment was based on the six sigma philosophy that the tolerances of the machinery would meet its customer’s requirements.
Aligning purchasing decisions with the customer’s Six Sigma requirements helped Southland make a better purchasing decision. The machinery it acquired reduced load/unload time, reduced cycle time, reduced scrap rates, and led to error-free loading. Selecting machinery that meets customer Six Sigma performance standards has helped Southland double its output while maintaining a high level of product quality
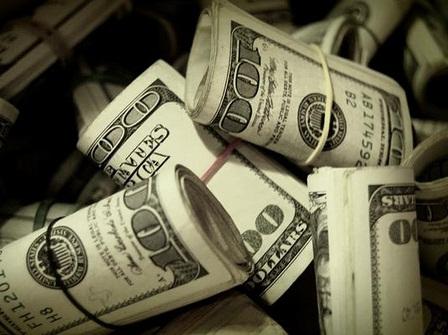
Many view Six Sigma as a collection of tools used to help measure and reduce variation in a production process. While accurate, this definition fails to fully capture the benefits that Six Sigma can provide to companies who use it. When Six Sigma is connected to a critical customer requirement such as higher product quality at Ford or meeting product tolerances at Southland, it can become instrumental in increasing revenue and profitability by increasing customer satisfaction..
The Six Sigma Approach
The Six Sigma methodology for solving problems is similar to many other approaches. What
makes Six Sigma standout from TQM is its project based approach and heavy use of
mathematical techniques and analysis. The mathematical techniques are central to Six
Sigma’s problem solving steps. The Define-Measure-Analyze-Improve-Control methodology
is adopted by Six Sigma for problem solving. It starts with the selection of projects, creation
of Teams and Project leaders and the signing of the Project charter and approval by the
Champion- in most cases - the Plant Head. This gives focus to improvement initiatives, by
clearly projecting the estimated savings and setting up of a time-frame. The selection of
projects themselves is based on robust criteria through, which it is possible to zero in on
projects that have high potential and require minimal efforts..
Six Sigma dovetails nicely with performance improvement initiatives intended to transform a
traditional manufacturing company into a lean supply chain operation. An effective Six
Sigma program results not just in tangible benefits like improved customer response time,
cut cycle times, product quality in engineering and performance but can also generate
revenue form intangible benefits based on improved customer satisfaction.
Good knowledge, clear communication, clarity on the subject ar e positives of the training, the ambience is good,flow,training linking one to one is appreciated. Should improve on the material given and needs a detailed cover.
I am identifying process which will be apt in the collection process. Suggest to give concept and flow in the starting itself.
S. Chandrasekar, Regional Manager, CITI Financials, Chennai
Does Toyota Really Have a Quality Issue?-Lean Six Sigma Perspective

Toyota's quality issues are far less severe, than what we are lead to believe, when compared to the other automobile manufacturers. However, from a Lean Six Sigma perspective, there is much work to be done and, here is the data to demonstrate this.We will start by looking at a comprehensive survey conducted in any e Initial Quality Study (IQS). IQS looks at the problem owners have reported during the first 90 days of owning a car. Participants of the study were asked to select from 228 potential problems with their vehicles from major malfunction to problems understanding controls.
Toyota, although not faring the best, does have one of the best records with respect to problems per 100 vehicles among over 20 vehicles included in the 2013 IQS survey. Although more years of data is required to see for certain if the quality trends observed in 2014 and 2015 are likely to continue, for now Toyota does seem to have better than average quality ratings relative to the overall automobile industry. That being said from a lean six sigma point of view, 88 defects per 100 vehicles is less than desirable. The goal for six sigma is 3.4 defects per million, which is drastically different than what Toyota is achieving today. In other words, Toyota has much to improve on its quality relative to the Lean Six Sigma standards. Perhaps it is time for Toyota and other car manufactures to focus more on six sigma (i.e. focus on quality) and less on Lean (i.e. focus on time). What do you think?
Six Sigma Course at Chennai
1st Sep to 1st Nov Black Belt Six Sigma, Online, WhatsApp: +91 98950 93119
E. : info@qualimations.com
Reg. Chennai: +91 9940622700
Reg.Online: Register for the Next Course