Overview
FMEA is a systematic group of activities intended to:
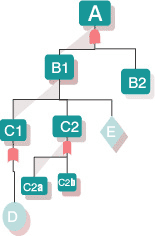
- * Recognize and evaluate the potential failure of a product or process and its effects.
- * FMEA is a simple, proactive approach which can help reduce the number of product failures that customers experience.
- * Identify actions which could eliminate or reduce the chance of the potential failure occurring.
- * Document the Failure analysis process.
Many companies use FMEA as a central pillar of their design process. FMEA provides a structured approach to the analysis of root causes (of failure), the estimation of severity or impact, and the effectiveness of strategies for prevention. The ultimate output is the generation of action plans to prevent, detect or reduce the impact of potential modes of failure. In a nutshell, it encourages the design team to consider:
- * What could go wrong and develop a ranked list of Failure Modes.
- * How badly it might go wrong
- * What needs to be done to prevent or mitigate the problem.
The basic logic can be applied at a number of levels, including organisational issues, strategy issues, product design issues, production processes and individual components. Typically, it is used to analyse either a product design or production process. An effective and affordable way to train your employees, FMEA is the perfect solution for busy people who can’t afford to spend days in a classroom. It allows you to schedule training when it is convenient... Read More
FAILURE MODE
A failure mode is the way in which a failure could occur and should not be confused with the complaints or issues. A failure mode is the root through which the failure has happened. This can also be mentioned as the deviation that has caused the effect.
EFFECT
The effect is related to the mode as the result of the mode in which the problem has happened. This result could be severe or major or minor.
CAUSE
The causes are related to the mode and is the reason why the deviation (failure Mode) has happened and hence the effect. Causes are generally well brainstormed before the possible list of causes to the failure mode is found
FAILURE MODE
When potential Failure mode is generated the list of failure modes must be continuously updated. This result in a failure mode database which can be used for subsequent analysis
The failure modes should be updated when a new symptom of the problem manifests and should be dynamic to the latest symptom of the problem.
The failure mode is the manner in which a component, Subsystem or System failed or failed to meet the purpose which it was intended to.
FMEA occurrence and detection rankings should be evolved out of a long term understanding of the issues and there revenue implications. The ranking given should be based on consensus.
Examples:
- * Poor logical skills
- * Frequent changes
- * Intermittent Operation
- * High Oxidation
- * Cracked fender
EFFECT
The effect quantification is very significant as the change from minor to major results in change in the severity rating and hence the priority of taking action on this failure mode.
The effect should be studied in depth to understand the severity of the problem. An assessment of the customer complaints is not enough.
The effect is the result of the failure mode as perceived by the internal and external customer.
The customers view is vital for the inference on the effect. The effect should clearly state whether it violates any codes and standards and these effects are no violation of safety standards.
Examples:
- * Wrong transfer of funds
- * Excess time to develop
- * Excess load time
- * Poor finish
- * Excess Noise
CAUSE
The cause list should be taken up for review continuously and any additional knowledge should be linked to the cause and classified as one that is up for controlling the failure of preventing them.
The cause identified should be established by facts and figures. The causes should be substantiated with assumptions and study and Test results.
The reason to the failure mode which when corrected results in the less or no deviation in the mode.
The list should mention every conceivable failure cause for each failure mode. The list should be aimed in such a way as the remedial action could be taken on them.
Examples:
- * In correct code
- * In correct design Specification
- * Less time for analysis
- * Incorrect Material quoted
- * Over stressing